تکنولوژی تولید ورق گالوانیزه: نوآوریها و پیشرفتهای اخیر
ورق گالوانیزه، که به ورقهای فولادی با روکش زینک گفته میشود، یکی از محصولات مهم در صنعت فولاد است. این فرآیند توسط دو متغیر اصلی، یعنی فولاد و زینک، که به ورق میپوشاند، انجام میشود. ترکیب این دو عنصر باعث ایجاد یک لایه محافظتی ضدخوردگی بر روی سطح فولاد میشود. در اینجا به برخی از نوآوریها و پیشرفتهای اخیر در تکنولوژی تولید ورق گالوانیزه اشاره میشود:
- فرآیند گالوانیزه حرارتی:فرآیند گالوانیزه حرارتی یکی از روشهای مهم در تولید ورقهای گالوانیزه است که با اعمال حرارت و فرآیندهای مربوطه، ورقهای فولادی به وسیلهٔ روکش زینک پوشانده میشوند. این فرآیند به عنوان گالوانیزه حرارتی یا گالوانیزه با استفاده از حرارت (Hot-Dip Galvanizing) نیز شناخته میشود. در زیر مراحل اصلی فرآیند گالوانیزه حرارتی توضیح داده شده است:
- آمادهسازی سطح فولاد:
- قبل از ورود به مرحله گالوانیزه حرارتی، ورقهای فولادی بازمیآیند و سطح آنها باید به دقت آماده شود. این مرحله شامل پاکسازی سطح از هر گونه ذرات، روغن، چربی، و اکسیدهای موجود است.
- غوطهور کردن در حمام اسیدی:
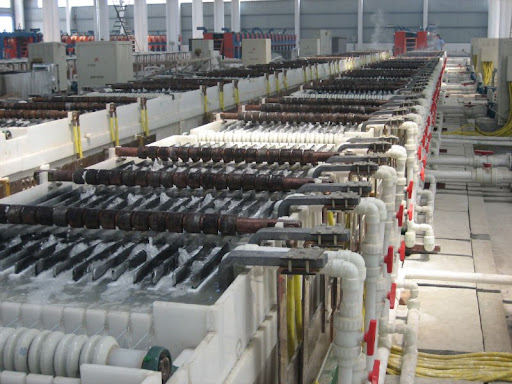
- ورقهای فولادی به داخل یک حمام اسیدی غوطهور میشوند تا هر گونه زنگ زدگی، روغن، و آلایندههای دیگر از سطح آنها حذف شود. این مرحله به نام پیشپالایش (Pickling) نیز شناخته میشود.
- آبکاری (Fluxing):
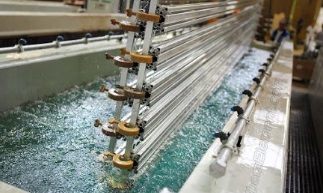
- پس از پیشپالایش، ورقها به آبکاری زیرکونیم کلراید (Zinc Ammonium Chloride) یا آبکاری کلرید آمونیوم زینک (Ammonium Zinc Chloride) غوطهور میشوند. این مرحله باعث ایجاد یک لایه تمیز بر روی سطح فولاد میشود و فرآیند گالوانیزه را تسهیل میکند.
- گالوانیزه حرارتی:
- ورقها به دماهای بسیار بالا (حدود 450-650 درجه سانتیگراد) درآورده میشوند. در این دما، روکش زینک از دستههای مذاب زینک به سطح فولاد میچسبد. این مرحله به نام گالوانیزه حرارتی شناخته میشود.
- خنککنندگی:
- ورقهای گالوانیزه حاصل پس از مرحله گالوانیزه حرارتی به سرعت خنک میشوند. این مرحله باعث ایجاد یک ساختار متریک و خود مرتب بین روکش زینک و سطح فولاد میشود.
- تمیزکاری و بازرسی:
- پس از خنکشدن، ورقها تمیز میشوند تا هر زنگ زدگی، ذرات زینک اضافی، و چربیهای احتمالی حذف شود. سپس یک بازرسی دقیق برای اطمینان از کیفیت روکش زینک انجام میشود.
- بستهبندی و ارسال:
- ورقهای گالوانیزه حاصل بستهبندی شده و برای ارسال به مقصد نهایی آماده میشوند.
گالوانیزه حرارتی یک فرآیند موثر و مقرون به صرفه برای حفاظت از فولاد در برابر خوردگی است. این فرآیند به دلیل ساختار یکپارچه ورقها و افزایش مقاومت به خوردگی در مقابل مواد خوراکی، هوا، و محیطهای خارجی دیگر، در صنایع ساختمانی، خودروسازی، صنعت دریایی، و غیره مورد استفاده قرار میگیرد.
- فرآیند گالوانیزه روکش چندلایه:
- در این فرآیند، ورقها به صورت چندلایه گالوانیزه میشوند. این بهبود نسبت به فرآیند گالوانیزه معمولی باعث افزایش ضریب پوشش زینک بر روی فولاد میشود و عمر مفید ورق گالوانیزه را افزایش میدهد.
- استفاده از تکنولوژی روکش الکتریکی:
تکنولوژی روکش الکتریکی یکی از روشهای نوآورانه در تولید ورقهای گالوانیزه است. در این روش، ذرات زینک به ورقها با استفاده از اصول الکتروفورز (Electrophoresis) یا روشهای مشابه الکتریکی میچسبند. این فرآیند به ورقها روکش زینکی بسیار یکنواخت و با کیفیت ایجاد میکند. در زیر توضیحاتی در مورد استفاده از تکنولوژی روکش الکتریکی در ورقهای گالوانیزه آورده شده است:
- الکتروفورز (Electrophoresis):
- در این فرآیند، ورقهای فولادی به عنوان الکترودها (الکترود مثبت) به حوضچهای حاوی محلول زینک اندوده میشوند. با اعمال جریان الکتریکی، ذرات زینک به سطح ورقها حرکت کرده و به صورت الکتریکی به آنها چسبیده و روکش میشوند.
- روکش الکتریکی با استفاده از محلولهای مایع:
- در این روش، ورقهای فولادی به طور همزمان در تعدادی حوضچه غوطهور میشوند که حاوی محلولهای مایع مانند محلولهای آلیای زینک هستند. با استفاده از فرآیند الکتریکی، ذرات زینک از محلول به سمت ورقها حرکت کرده و روکش میشوند.
- استفاده از تکنولوژیهای حفاظتی:
- در تکنولوژی روکش الکتریکی، معمولاً از تکنولوژیهای حفاظتی برای جلوگیری از تجمع ذرات زینک در ناحیههای خاصی از ورق استفاده میشود. این تکنولوژیها میتوانند به توزیع یکنواخت ذرات زینک در سطح ورق کمک کرده و کیفیت روکش را بهبود بخشند.
- کنترل دقیق فرآیند:
- استفاده از سیستمهای کنترل الکترونیکی و هوشمند در فرآیند روکش الکتریکی میتواند به کنترل دقیقتر و بهبود کیفیت روکش زینک منجر شود.
- محافظت زیستمحیطی:
- از آنجایی که این فرآیند توسط جریان الکتریکی انجام میشود و به صورت الکتریکی به ورقها چسبیده میشود، کمترین مقدار زینک مصرف میشود. این موضوع به افزایش بهرهوری و کاهش پسماند زینک منجر میشود.
استفاده از تکنولوژی روکش الکتریکی در تولید ورقهای گالوانیزه بهبودهایی در مسائل مانند یکنواختی روکش، کاهش مصرف مواد و افزایش کنترل فرآیند به دنبال داشته است. این روش به عنوان یک رویکرد مؤثر برای بهبود کیفیت ورقهای گالوانیزه در صنایع مختلف شناخته شده است.
- گالوانیزه مستقیم در خطوط تولید فولاد:
گالوانیزه مستقیم در خطوط تولید فولاد به معنای اجرای فرآیند گالوانیزه در خطوط تولید فولاد میباشد، به طوری که تمام فرآیند از تولید فولاد تا گالوانیزه شدن در یک خط تولید یکپارچه انجام میشود. این رویکرد از لحاظ عملکرد و بهینگی فرآیند تولید مزایایی را فراهم میکند.
مراحل اجرای گالوانیزه مستقیم در خطوط تولید فولاد میتواند به شکل زیر باشد:
- آمادهسازی ورق فولادی:
- در ابتدا، ورقهای فولادی به خط تولید وارد میشوند و از هرگونه ذرات، چربی، یا زنگزدگی پاکسازی میشوند.
- پیشپالایش (پیشتصفیه):
- ورقها به حوضچههای پیشپالایش میروند که ممکن است شامل حمامهای اسیدی باشد. این مرحله به منظور حذف اکسیدها و ذرات ناخواسته از سطح ورق است.
- غوطهور کردن در حوضچه گالوانیزه:
- سپس ورقها به حوضچههای گالوانیزه مستقیم وارد میشوند. این حوضچه شامل محلول زینک مذاب است. ورقها تا مدتی در این حوضچه قرار میگیرند تا روکش زینک از طریق غوطهور شدن به سطح آنها چسبیده و جامد شود.
- خنککنندگی:
- پس از غوطهور شدن و روکش زینک به سطح ورق چسبیدند، ورقها به سرعت از حوضچه خارج میشوند و به سرعت خنک میشوند.
- تمیزکاری و بازرسی:
- ورقها تمیز میشوند تا از هر ذرات زینک اضافی خالی شوند و سپس تحت بازرسی قرار میگیرند. این بازرسی به منظور اطمینان از کیفیت و یکنواختی روکش زینک است.
- بستهبندی و ارسال:
- در نهایت، ورقهای گالوانیزه حاصل بستهبندی میشوند و برای ارسال به بازار آماده میشوند.
استفاده از گالوانیزه مستقیم در خطوط تولید فولاد دارای مزایایی مانند کاهش هزینهها، بهینهسازی زمان و فضا، و افزایش بهرهوری میباشد. این رویکرد به ویژه در صنایعی که نیاز به فولاد گالوانیزه دارند، مانند صنعت ساختمان و خودروسازی، مورد توجه قرار گرفته است.
- توسعه روشهای ضدکریستالیزه:
- مشکل اصلی در ورقهای گالوانیزه در برخی از شرایط، مانند محیطهای خورنده و یا در دماهای خاص، کریستالیزه شدن زینک است. تحقیقات در زمینه توسعه روشهای ضدکریستالیزه بهبودهایی در مقاومت به خوردگی ورقهای گالوانیزه ایجاد کرده است.
- استفاده از آلیاژهای جدید:
- به منظور بهبود خصوصیات ورقهای گالوانیزه، آلیاژهای جدید زینک با المانهای دیگر مورد استفاده قرار گرفتهاند. این آلیاژها میتوانند خصوصیات ضدخوردگی و مکانیکی را بهبود بخشند.
- سیستمهای ردیابی و کنترل خودکار:
- استفاده از سیستمهای هوشمند و کنترل خودکار در خطوط تولید و گالوانیزهسازی بهبود قابلیت کنترل، دقت، و کارایی در تولید ورقهای گالوانیزه ایجاد کرده است.
با توجه به پیشرفتهای تکنولوژی در صنعت فولاد و گالوانیزه، انتظار میرود که نوآوریهای بیشتری در آینده به وجود آیند. این پیشرفتها به بهبود خصوصیات و عملکرد و
تکنولوژی تولید ورق گالوانیزه: نوآوریها و پیشرفتهای اخیر
ورق گالوانیزه، که به ورقهای فولادی با روکش زینک گفته میشود، یکی از محصولات مهم در صنعت فولاد است. این فرآیند توسط دو متغیر اصلی، یعنی فولاد و زینک، که به ورق میپوشاند، انجام میشود. ترکیب این دو عنصر باعث ایجاد یک لایه محافظتی ضدخوردگی بر روی سطح فولاد میشود. در اینجا به برخی از نوآوریها و پیشرفتهای اخیر در تکنولوژی تولید ورق گالوانیزه اشاره میشود:
- فرآیند گالوانیزه حرارتی:
فرآیند گالوانیزه حرارتی یکی از روشهای مهم در تولید ورقهای گالوانیزه است که با اعمال حرارت و فرآیندهای مربوطه، ورقهای فولادی به وسیلهٔ روکش زینک پوشانده میشوند. این فرآیند به عنوان گالوانیزه حرارتی یا گالوانیزه با استفاده از حرارت (Hot-Dip Galvanizing) نیز شناخته میشود. در زیر مراحل اصلی فرآیند گالوانیزه حرارتی توضیح داده شده است:
- آمادهسازی سطح فولاد:
- قبل از ورود به مرحله گالوانیزه حرارتی، ورقهای فولادی بازمیآیند و سطح آنها باید به دقت آماده شود. این مرحله شامل پاکسازی سطح از هر گونه ذرات، روغن، چربی، و اکسیدهای موجود است.
- غوطهور کردن در حمام اسیدی:
- ورقهای فولادی به داخل یک حمام اسیدی غوطهور میشوند تا هر گونه زنگ زدگی، روغن، و آلایندههای دیگر از سطح آنها حذف شود. این مرحله به نام پیشپالایش (Pickling) نیز شناخته میشود.
- آبکاری (Fluxing):
- پس از پیشپالایش، ورقها به آبکاری زیرکونیم کلراید (Zinc Ammonium Chloride) یا آبکاری کلرید آمونیوم زینک (Ammonium Zinc Chloride) غوطهور میشوند. این مرحله باعث ایجاد یک لایه تمیز بر روی سطح فولاد میشود و فرآیند گالوانیزه را تسهیل میکند.
- گالوانیزه حرارتی:
- ورقها به دماهای بسیار بالا (حدود 450-650 درجه سانتیگراد) درآورده میشوند. در این دما، روکش زینک از دستههای مذاب زینک به سطح فولاد میچسبد. این مرحله به نام گالوانیزه حرارتی شناخته میشود.
- خنککنندگی:
- ورقهای گالوانیزه حاصل پس از مرحله گالوانیزه حرارتی به سرعت خنک میشوند. این مرحله باعث ایجاد یک ساختار متریک و خود مرتب بین روکش زینک و سطح فولاد میشود.
- تمیزکاری و بازرسی:
- پس از خنکشدن، ورقها تمیز میشوند تا هر زنگ زدگی، ذرات زینک اضافی، و چربیهای احتمالی حذف شود. سپس یک بازرسی دقیق برای اطمینان از کیفیت روکش زینک انجام میشود.
- بستهبندی و ارسال:
- ورقهای گالوانیزه حاصل بستهبندی شده و برای ارسال به مقصد نهایی آماده میشوند.
گالوانیزه حرارتی یک فرآیند موثر و مقرون به صرفه برای حفاظت از فولاد در برابر خوردگی است. این فرآیند به دلیل ساختار یکپارچه ورقها و افزایش مقاومت به خوردگی در مقابل مواد خوراکی، هوا، و محیطهای خارجی دیگر، در صنایع ساختمانی، خودروسازی، صنعت دریایی، و غیره مورد استفاده قرار میگیرد.
- .
- فرآیند گالوانیزه روکش چندلایه:
- در این فرآیند، ورقها به صورت چندلایه گالوانیزه میشوند. این بهبود نسبت به فرآیند گالوانیزه معمولی باعث افزایش ضریب پوشش زینک بر روی فولاد میشود و عمر مفید ورق گالوانیزه را افزایش میدهد.
- استفاده از تکنولوژی روکش الکتریکی:
تکنولوژی روکش الکتریکی یکی از روشهای نوآورانه در تولید ورقهای گالوانیزه است. در این روش، ذرات زینک به ورقها با استفاده از اصول الکتروفورز (Electrophoresis) یا روشهای مشابه الکتریکی میچسبند. این فرآیند به ورقها روکش زینکی بسیار یکنواخت و با کیفیت ایجاد میکند. در زیر توضیحاتی در مورد استفاده از تکنولوژی روکش الکتریکی در ورقهای گالوانیزه آورده شده است:
- الکتروفورز (Electrophoresis):
- در این فرآیند، ورقهای فولادی به عنوان الکترودها (الکترود مثبت) به حوضچهای حاوی محلول زینک اندوده میشوند. با اعمال جریان الکتریکی، ذرات زینک به سطح ورقها حرکت کرده و به صورت الکتریکی به آنها چسبیده و روکش میشوند.
- روکش الکتریکی با استفاده از محلولهای مایع:
- در این روش، ورقهای فولادی به طور همزمان در تعدادی حوضچه غوطهور میشوند که حاوی محلولهای مایع مانند محلولهای آلیای زینک هستند. با استفاده از فرآیند الکتریکی، ذرات زینک از محلول به سمت ورقها حرکت کرده و روکش میشوند.
- استفاده از تکنولوژیهای حفاظتی:
- در تکنولوژی روکش الکتریکی، معمولاً از تکنولوژیهای حفاظتی برای جلوگیری از تجمع ذرات زینک در ناحیههای خاصی از ورق استفاده میشود. این تکنولوژیها میتوانند به توزیع یکنواخت ذرات زینک در سطح ورق کمک کرده و کیفیت روکش را بهبود بخشند.
- کنترل دقیق فرآیند:
- استفاده از سیستمهای کنترل الکترونیکی و هوشمند در فرآیند روکش الکتریکی میتواند به کنترل دقیقتر و بهبود کیفیت روکش زینک منجر شود.
- محافظت زیستمحیطی:
- از آنجایی که این فرآیند توسط جریان الکتریکی انجام میشود و به صورت الکتریکی به ورقها چسبیده میشود، کمترین مقدار زینک مصرف میشود. این موضوع به افزایش بهرهوری و کاهش پسماند زینک منجر میشود.
استفاده از تکنولوژی روکش الکتریکی در تولید ورقهای گالوانیزه بهبودهایی در مسائل مانند یکنواختی روکش، کاهش مصرف مواد و افزایش کنترل فرآیند به دنبال داشته است. این روش به عنوان یک رویکرد مؤثر برای بهبود کیفیت ورقهای گالوانیزه در صنایع مختلف شناخته شده است.
- .
- گالوانیزه مستقیم در خطوط تولید فولاد:
گالوانیزه مستقیم در خطوط تولید فولاد به معنای اجرای فرآیند گالوانیزه در خطوط تولید فولاد میباشد، به طوری که تمام فرآیند از تولید فولاد تا گالوانیزه شدن در یک خط تولید یکپارچه انجام میشود. این رویکرد از لحاظ عملکرد و بهینگی فرآیند تولید مزایایی را فراهم میکند.
مراحل اجرای گالوانیزه مستقیم در خطوط تولید فولاد میتواند به شکل زیر باشد:
- آمادهسازی ورق فولادی:
- در ابتدا، ورقهای فولادی به خط تولید وارد میشوند و از هرگونه ذرات، چربی، یا زنگزدگی پاکسازی میشوند.
- پیشپالایش (پیشتصفیه):
- ورقها به حوضچههای پیشپالایش میروند که ممکن است شامل حمامهای اسیدی باشد. این مرحله به منظور حذف اکسیدها و ذرات ناخواسته از سطح ورق است.
- غوطهور کردن در حوضچه گالوانیزه:
- سپس ورقها به حوضچههای گالوانیزه مستقیم وارد میشوند. این حوضچه شامل محلول زینک مذاب است. ورقها تا مدتی در این حوضچه قرار میگیرند تا روکش زینک از طریق غوطهور شدن به سطح آنها چسبیده و جامد شود.
- خنککنندگی:
- پس از غوطهور شدن و روکش زینک به سطح ورق چسبیدند، ورقها به سرعت از حوضچه خارج میشوند و به سرعت خنک میشوند.
- تمیزکاری و بازرسی:
- ورقها تمیز میشوند تا از هر ذرات زینک اضافی خالی شوند و سپس تحت بازرسی قرار میگیرند. این بازرسی به منظور اطمینان از کیفیت و یکنواختی روکش زینک است.
- بستهبندی و ارسال:
- در نهایت، ورقهای گالوانیزه حاصل بستهبندی میشوند و برای ارسال به بازار آماده میشوند.
استفاده از گالوانیزه مستقیم در خطوط تولید فولاد دارای مزایایی مانند کاهش هزینهها، بهینهسازی زمان و فضا، و افزایش بهرهوری میباشد. این رویکرد به ویژه در صنایعی که نیاز به فولاد گالوانیزه دارند، مانند صنعت ساختمان و خودروسازی، مورد توجه قرار گرفته است.
- .
- توسعه روشهای ضدکریستالیزه:
- مشکل اصلی در ورقهای گالوانیزه در برخی از شرایط، مانند محیطهای خورنده و یا در دماهای خاص، کریستالیزه شدن زینک است. تحقیقات در زمینه توسعه روشهای ضدکریستالیزه بهبودهایی در مقاومت به خوردگی ورقهای گالوانیزه ایجاد کرده است.
- استفاده از آلیاژهای جدید:
- به منظور بهبود خصوصیات ورقهای گالوانیزه، آلیاژهای جدید زینک با المانهای دیگر مورد استفاده قرار گرفتهاند. این آلیاژها میتوانند خصوصیات ضدخوردگی و مکانیکی را بهبود بخشند.
- سیستمهای ردیابی و کنترل خودکار:
- استفاده از سیستمهای هوشمند و کنترل خودکار در خطوط تولید و گالوانیزهسازی بهبود قابلیت کنترل، دقت، و کارایی در تولید ورقهای گالوانیزه ایجاد کرده است.
با توجه به پیشرفتهای تکنولوژی در صنعت فولاد و گالوانیزه، انتظار میرود که نوآوریهای بیشتری در آینده به وجود آیند. این پیشرفتها به بهبود خصوصیات و عملکرد و
مقاومت ورقهای گالوانیزه در برابر خوردگی و سایر خصوصیات آنها ارتقاء خواهد داد.
مقاومت ورقهای گالوانیزه در برابر خوردگی و سایر خصوصیات آنها ارتقاء خواهد داد.